Deutz Italy e Faresin hanno sottoscritto un accordo di partnership che è anche un possibile modello di evoluzione per l’intero settore delle macchine per il construction. Ne parliamo con Rudi Alborghetti, Aftersales & Service Director di Deutz Italy.
E’ una formula di collaborazione inedita e innovativa. Pensata per portare le tradizionali relazioni fra OEM e costruttori di macchine operatrici su nuovi livelli di efficienza e operatività. A lanciarla sono due brand come Deutz Italy e Faresin, il primo fra i più prestigiosi costruttori di motori a livello mondiale, la seconda una solida realtà nel settore del sollevamento, che hanno recentemente siglato un importante contratto di cooperazione strategica per la distribuzione di ricambi e per estendere il servizio di assistenza tecnica sulle macchine Faresin in Lombardia.
Grazie a questo accordo si rafforzerà la presenza sul territorio dell’assistenza post-vendita, rendendo più veloce e puntuale il servizio al cliente, e al tempo stesso Deutz Italy diventerà un centro autorizzato Faresin. In questa veste, Deutz potrà rivendere i ricambi originali e effettuare operazioni di manutenzione e riparazione non solo sui motori Deutz installati sui carri miscelatori e i sollevatori telescopici Faresin, ma anche sull’intera macchina. Commentando la firma dell’accordo Giulia Faresin, Operations Manager dell’azienda, aveva già sottolineato come Faresin stia investendo molto nelle soluzioni digitali 4.0 e nel potenziamento dei supporti agli utilizzatori, e che in questa ottica l’accordo con Deutz è finalizzato a intervenire proprio sulla capillarità territoriale delle officine autorizzate, consentendo al service di raggiungere più facilmente i clienti lombardi abbreviando i tempi di intervento e riparazione. Per conoscere più nel dettaglio come si svilupperà dal punto di vista operativo questa nuova partnership abbiamo incontrato Rudi Alborghetti, Aftersales & Service Director di Deutz Italy.
Partnership win win
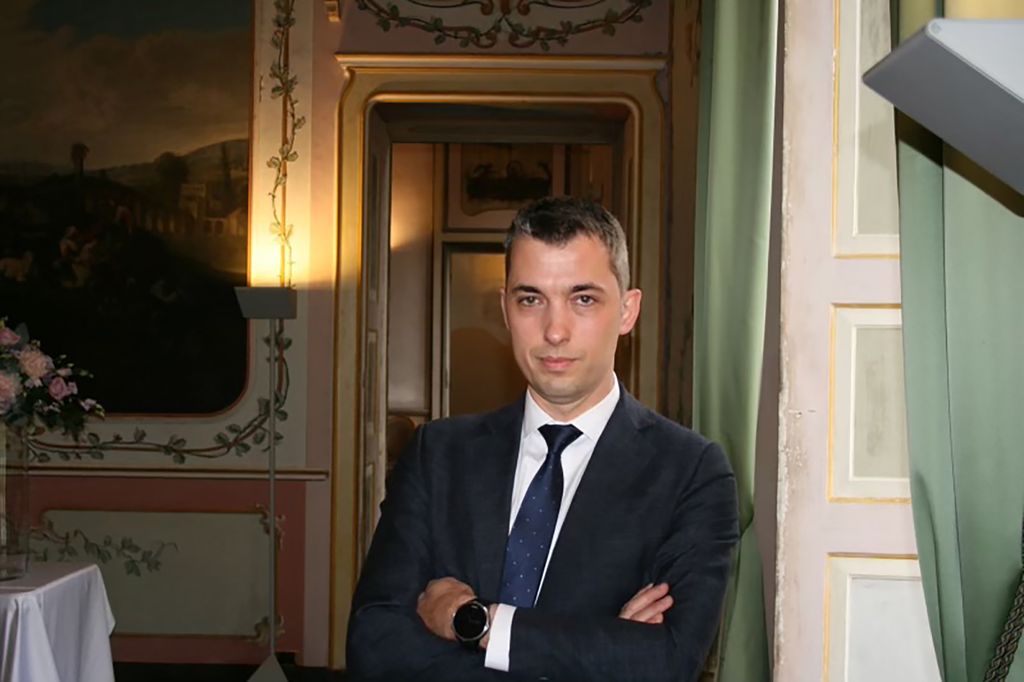
La formula di collaborazione che avete scelto è per certi versi inedita nel nostro paese: su quali basi è nato questo accordo?
Deutz era da tempo fornitore di motori diesel per le macchine Faresin, ma come lei ha sottolineato questa partnership introduce importanti elementi di novità nei tradizionali rapporti fra OEM e costruttore, e in particolare scaturisce da una visione strategica da noi sviluppata in questi ultimi anni. Visione che a sua volta deriva dal fatto che Deutz è un costruttore di motori “puro”, e non disponendo di un mercato captive da alimentare si contraddistingue per una naturale proiezione verso quello esterno. Per quanto riguarda in particolare l’assistenza, pur avendo sempre lavorato esclusivamente sui motori installati sulle macchine Faresin abbiamo sviluppato nel tempo una approfondita conoscenza delle loro caratteristiche, e questo, unitamente al fatto che l’area dell’assistenza e manutenzione rappresenta una voce sempre più importante sia in termini di supporto al cliente che di fatturato, è stato il punto di partenza da cui ha avuto origine questo nuovo modello di collaborazione. In base all’accordo, in particolare, Deutz Italy si occuperà degli interventi sulla totalità della macchina, formando a questo scopo in collaborazione con Faresin uno staff di tecnici specializzati e mettendo a disposizione dell’azienda la propria capillare rete di assistenza con importanti vantaggi reciproci. Da un lato, Faresin accrescerà nettamente la sua presenza sul territorio, dall’altro Deutz, oltre ad occuparsi dell’assistenza, diventerà dealer autorizzato del marchio. In questa prima fase i servizi di assistenza e vendita ricambi sono erogati esclusivamente dalla nostra officina centrale, ma l’accordo prevede una progressiva estensione della formula a tutti i centri della rete di Deutz Italy. Tutto questo in linea con una progressiva evoluzione del mercato che vede la macchina operatrice come una commodity e il service in posizione sempre più strategica sia in termini di supporto al cliente che di redditività.
L’evoluzione del motore secondo Deutz
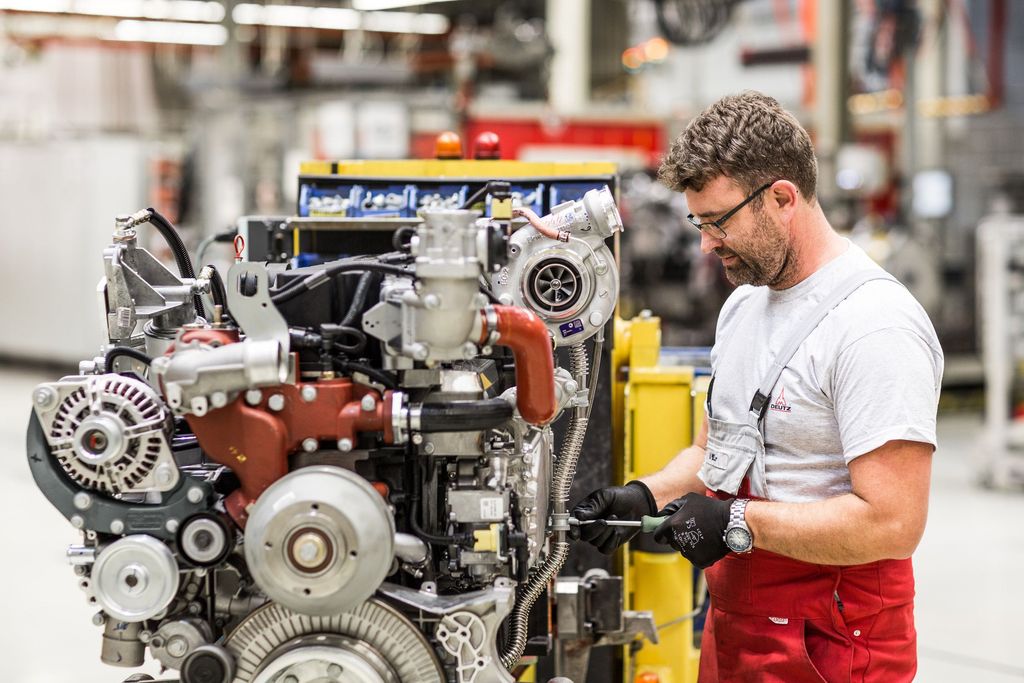
A questo proposito, il settore motoristico ha vissuto in questi anni una serie di importanti trasformazioni stimolate dal continuo aggiornamento degli step regolamentari in materia di emissioni: qual è lo stato dell’arte, e in quale direzione si sta evolvendo il motore termico in casa Deutz?
Salvo pochissime eccezioni tutte le nostre gamme di propulsori sono allineate allo Stage V e il prossimo orizzonte, comunque ancora piuttosto lontano nel tempo, è lo Stage VI. Parallelamente a questa linea di sviluppo oggi l’attenzione è focalizzata soprattutto sulle tecnologie ibride e full electric, con formule che nell’ottica di una progressiva riduzione dell’utilizzo di combustibili fossili sono orientate a un calibrato downgrade delle cilindrate e delle potenze a parità di prestazioni, tendenza ormai sperimentata con successo sui tradizionali motori endotermici, con un utilizzo del propulsore eminentemente dedicato alla carica dei pacchi batterie a bordo macchina è un’usura nettamente inferiore in quanto quest’ultimo lavora prevalentemente a regime costante e in maniera più efficiente. Naturalmente il fronte di questi sviluppi è molto articolato e coinvolge molteplici tecnologie, ma in linea generale questo è l’orizzonte su cui si stanno concentrando gli sforzi del settore motoristico, anche in collaborazione con alcuni importanti costruttori. Ci sono poi tecnologie futuribili come quelle basate sull’alimentazione a idrogeno, estremamente promettenti ma che richiederanno ancora diverso tempo per entrare nella fase di produzione industrializzata per motivi legati soprattutto a costi di produzione e disponibilità di rete. Si tratta comunque di una soluzione dalle grandi potenzialità e su cui Deutz sta investendo in maniera importante: al momento è già stato realizzato un prototipo da 200 kW di potenza, e altri sono già in fase di sviluppo.
Si guarda al futuro
Da parte dei costruttori con cui lavorate c’è sensibilità verso queste evoluzioni tecnologiche?
Dipende molto dal settore di applicazione. Nell’ambito della logistica, ad esempio, la presenza dell’elettrico è ormai una realtà consolidata da decenni in quanto questa alimentazione presenta caratteristiche ideali per questo ambito operativo sia in termini di performance che di assenza di emissioni, mentre il settore industrial è al momento focalizzato soprattutto sull’implementazione di questa tecnologia sulle macchine di piccola taglia, principalmente per motivi legati a potenze e curve di erogazione oltre che alla effettiva disponibilità di punti di ricarica. In ambito cittadino, ad esempio, il miniescavatore elettrico trova un utilizzo ideale ed è ormai una realtà, come del resto dimostrano le sempre più numerose proposte presenti sul mercato, sia ibride che full electric, e in questo segmento le prospettive di sviluppo sono senza dubbio molto interessanti. Salendo a quelli superiori, invece, le tecnologie attualmente disponibili non sono ancora sufficientemente sviluppate per permettere l’implementazione dell’alimentazione elettrica a profili di carico e di utilizzo che al momento possono ancora essere soddisfatte solo dal tradizionale motore endotermico. In linea generale non c’è comunque dubbio che fra le tecnologie alternative questa sia quella concretamente più promettente, e in questa ottica Deutz ha compiuto importanti investimenti, anche attraverso l’acquisizione di realtà esterne, allo scopo di raggiungere un’autonomia totale nello sviluppo in house di soluzioni sia ibride che full electric. I tempi sono senza dubbio maturi per compiere ulteriori passi in questa direzione.
Ma il diesel non è morto
Allo stesso tempo, come lei stesso ha accennato, il motore endotermico non ha ancora detto la sua ultima parola…
Senza alcun dubbio. Esistono ancora importanti margini di sviluppo e affinamento sotto diversi aspetti, ad esempio un’ulteriore ottimizzazione dell’efficienza e del rendimento, l’utilizzo di nuovi materiali, l’affinamento dell’elettronica di gestione. Il motore endotermico ha ancora una vita molto lunga davanti a sé, soprattutto negli ambiti applicativi più impegnativi; con ogni probabilità vedremo proseguire alcune tendenze come il già accennato downgrade delle cilindrate e delle dimensioni a fronte di un aumento delle potenze, lavorando ad esempio sull’ottimizzazione delle turbine, la sovralimentazione, il raffreddamento, i sistemi di iniezione, anche nell’ottica di una sempre più agevole ingegnerizzazione delle macchine di destinazione.