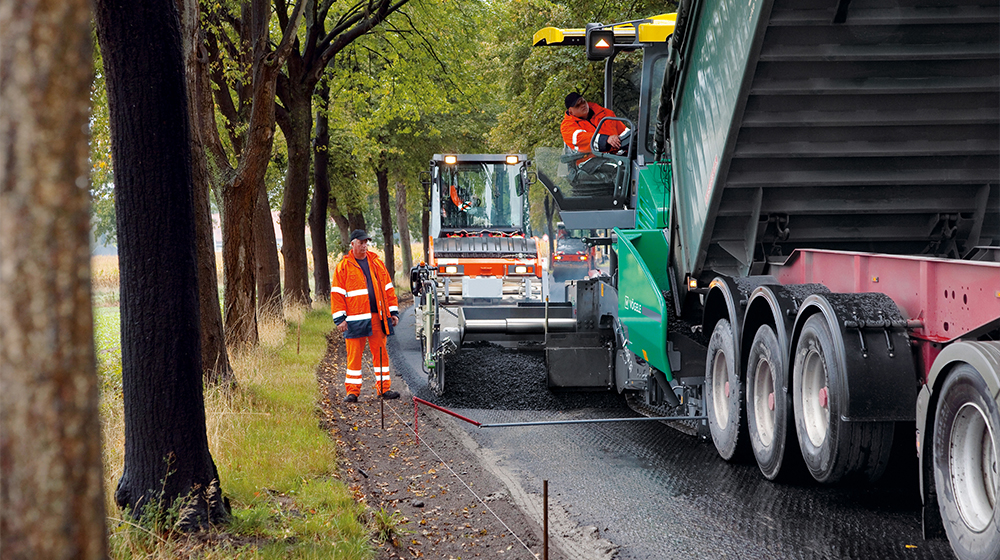
Per produrre con aggregati e bitume degli asfalti per la pavimentazione stradale è necessario un processo di miscelazione termica. A questo scopo è indispensabile un impianto di miscelazione asfalto.
Questo significa anche che milioni di tonnellate di asfalto devono essere asportate. Questo compito è svolto principalmente dalle frese a freddo, che sono il primo anello della filiera di processo, al quale seguono nel passo successivo gli impianti di frantumazione e vagliatura e gli impianti di miscelazione asfalto; al termine della filiera, l’asfalto viene nuovamente steso dalle finitrici quale parte del nuovo conglomerato.
La sfida: aumentare l’asfalto di recupero
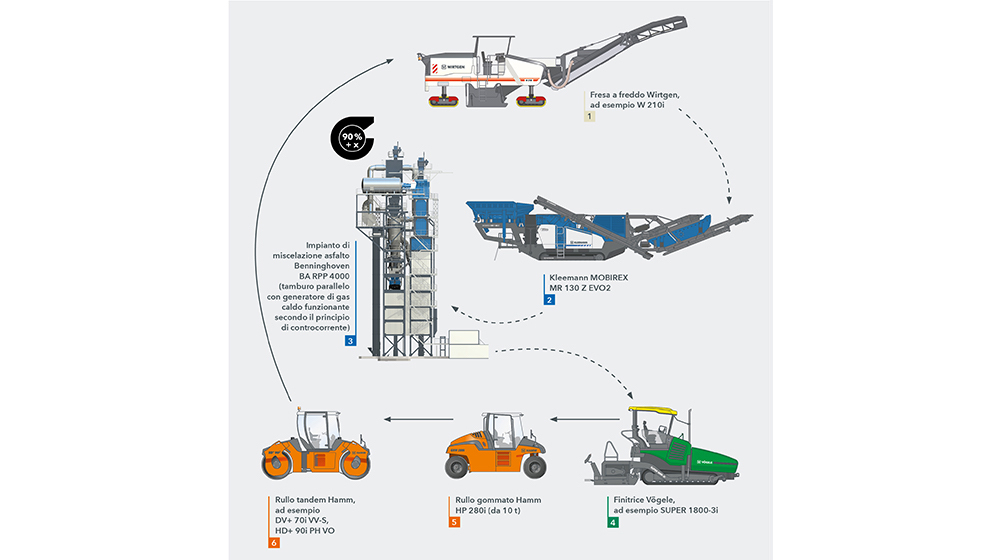
In molti Paesi, è rarissimo che nei cantieri si incontri un camion carico di conglomerato che non contenga una quota di asfalto riciclato. Nel 2018, nella sola Germania, un quarto dell’asfalto prodotto (41 milioni di tonnellate) è stato rappresentato dall’asfalto di recupero (10,5 milioni di tonnellate). Alla luce di una quantità totale di asfalto di recupero pari a 12 milioni di tonnellate, lo scorso anno la quota di riutilizzo è stata pari all’87%.
Il trattamento dell’asfalto è una scelta di politica economica per la preservazione delle risorse naturali. L’industria cerca pertanto costantemente soluzioni in grado di ottimizzare i processi all’interno degli impianti di miscelazione asfalto. Un concetto importante al riguardo è l’aumento della quantità aggiunta di asfalto di recupero in tutte le ricette delle tecnologie di trattamento “a caldo e freddo”. La quantità aggiunta massima non protegge solo l’ambiente, ma presenta anche dei vantaggi per i prezzi del conglomerato.
Nel classico sistema di riciclaggio con tamburo parallelo in flusso equicorrente la temperatura è limitata a 130 °C per via delle emissioni allo scarico prodotte, ma per ragioni fisiche le temperature dei gas di scarico sono superiori, con un conseguente aumento del consumo di energia e del carico di lavoro della depolverizzazione. Per raggiungere una temperatura del conglomerato di 160 °C, in questo caso, occorre surriscaldare i minerali bianchi.
Una soluzione controcorrente
Nel tamburo di riciclo con generatore di gas caldo, diversamente dal classico tamburo parallelo per il riciclaggio, il materiale riciclabile viene riscaldato indirettamente nel procedimento in controcorrente. In questo caso, il materiale fluisce nel tamburo in direzione opposta alla sorgente di calore. In questo modo vengono ottenute temperature del materiale maggiori con una contemporanea riduzione della temperatura dei gas di scarico. La temperatura di uscita di 160 °C corrisponde alla temperatura dell’ulteriore lavorazione, la temperatura dei gas di scarico rimane al di sopra del punto di rugiada a 100 °C circa. Tutto questo è possibile solo grazie all’impiego di un generatore di gas caldo, in quanto, in caso di riscaldamento diretto, il materiale riciclabile brucerebbe e sarebbe quindi inutilizzabile. Bruciatore, generatore di gas caldo, tamburo di riciclo, cappa di aspirazione e sistema dell’aria ricircolata e dell’aria di scarico sono precisamente coordinati. Effetto positivo: i minerali bianchi non devono più essere surriscaldati, con una conseguente notevole riduzione dell’energia necessaria. Attraverso il riciclaggio con procedimento in controcorrente, le emissioni possono essere ridotte notevolmente (regolamento TA LUFT) e, a seconda della qualità del materiale riciclabile, è possibile ottenere quote di materiale riciclabile del 90 + X%. Questo rende particolarmente interessante l’investimento in questa tecnologia tanto verde quanto efficiente.
La tecnologia diventa ancora più verde se anche i passi del processo a monte – lavorazione della curva granulometrica e fresatura dell’asfalto – vengono convertiti ai procedimenti e alle tecnologie più moderne.
Il segreto è nell’impianto di vagliatura
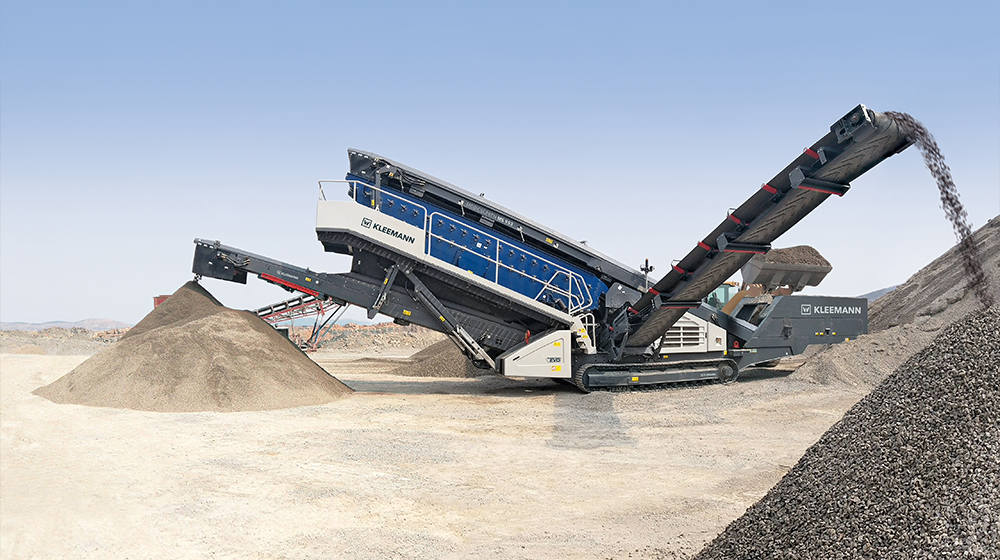
La quantità aggiunta massima teoricamente possibile di asfalto di recupero dipende notevolmente dalla relativa curva granulometrica – in altre parole, dalle sostanze contenute in termini di quantità, dimensioni e composizione. Un obiettivo deve quindi essere quello di avvicinare il più possibile la curva granulometrica dell’asfalto di recupero frantumato alla curva granulometrica desiderata del prodotto finito ovvero dell’asfalto pronto. In questo caso sono necessari degli impianti di vagliatura semoventi, che garantiscono che fino all’80% dell’asfalto di recupero (fresato) possa essere trattato direttamente. In questo modo si abbattono notevolmente i costi di processo rispetto a un trattamento completo del fresato.
Nel caso di un trattamento completo, comprendente quindi anche il residuo di vagliatura, dovrebbero essere impiegati anche dei frantoi a urto dotati di un’unità di vagliatura a valle.
Con Wirtgen la fresatura è intelligente
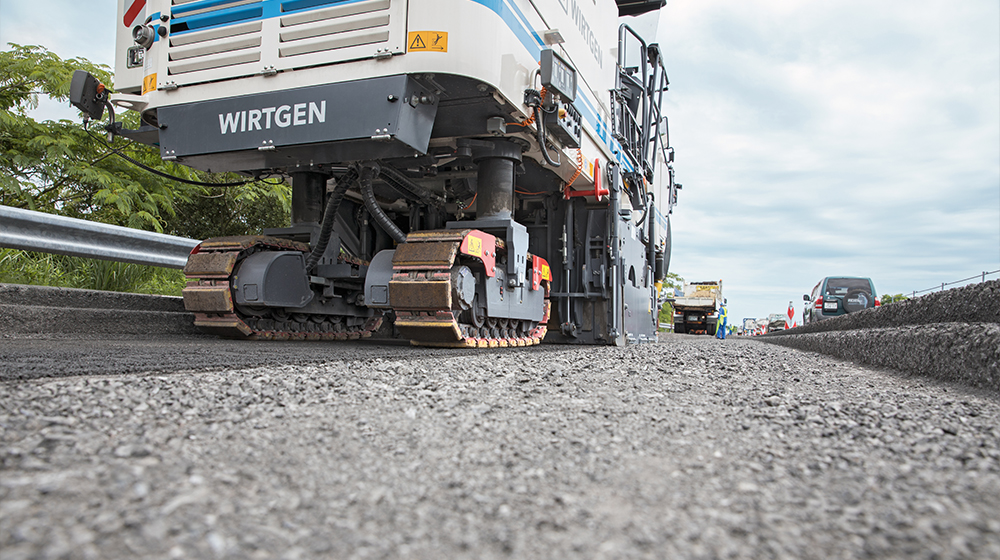
Tenendo in considerazione anche il fattore della tecnologia di fresatura intelligente, utilizzato da Wirtgen, il riutilizzo economico del granulato di fresatura nell’impianto di miscelazione asfalto viene aumentato ulteriormente. Il merito di tutto ciò è in misura notevole dell’irrorazione d’acqua in funzione del carico delle frese a freddo. L’acqua necessaria per il raffreddamento dei denti per fresatura viene regolata in base al carico del motore e alla velocità di fresatura. Grazie all’attivazione automatica dell’impianto acqua all’abbassamento del tamburo di fresatura ovvero alla disattivazione automatica al momento dello stop dei lavori di fresatura, il consumo d’acqua può essere notevolmente ridotto. Concretamente, è possibile risparmiare fino al 20% di acqua. A conti fatti, ciò significa che la durata utile dei denti per fresatura viene prolungata, la fresa a freddo deve essere rifornita meno spesso e i tempi di fermo sono inferiori. Questo non fa felice solo l’operatore della fresa, ma anche il capo produzione dell’impianto di miscelazione asfalto, che tra beneficio dal minor consumo di acqua, in quanto questo comporta un’umidità residua del granulato fresato inferiore del 3-4% per tonnellata di asfalto. Senza l’impiego delle più moderne tecnologie di fresatura, l’umidità residua sarebbe maggiore.
Per i processi di asciugatura necessari per la produzione del nuovo asfalto nell’impianto di miscelazione asfalto, l’equazione è semplice: un materiale di partenza più asciutto dell’1% risparmia 1 l di olio combustibile per tonnellata di asfalto pronto nella lavorazione del conglomerato riciclabile. A questo si aggiunge il fatto che il minore fabbisogno energetico riduce le emissioni di CO2.