Si è recentemente concluso il rifacimento completo delle piste dell’aeroporto di Orio al Serio utilizzando quattro vibrofinitrici BF800 C, quattro rulli tandem BW 174 AP-4i AM e un rullo gommato BW 27 RH-4i. Tutto di Bomag.
Il cielo è l’elemento degli aerei, ma la terra – e in particolare le piste di decollo e di atterraggio – rappresenta la via d’accesso a quell’aria che, ogni giorno, sostiene milioni di viaggiatori. Va da sé che la manutenzione delle piste degli aeroporti sia di assoluta importanza e rappresenti uno snodo fondamentale per comprendere la sicurezza di qualsiasi aeroporto. Per questo la Sacbo, Società per l’Aeroporto Civile di Bergamo Orio al Serio ha deciso di investire sul completo rifacimento delle piste del terzo aeroporto lombardo, per le quali sono state utilizzate diverse macchine Bomag.
Il cantiere
L’infrastruttura aeroportuale bergamasca è caratterizzata da una pista lunga circa 3 km, per una larghezza pavimentata di 60 m, cui si aggiungono il piazzale principale posto a sud del sedime, un piazzale secondario di minori dimensioni, la via di rullaggio T e i raccordi denominati A, B, C, D, E, ed F.
I lavori di manutenzione straordinaria si sono concentrati principalmente sulla riqualifica della pavimentazione di tutta la pista, delle vie di rullaggio e dei raccordi. A questi si sono aggiunti il rifacimento delle opere civili, degli impianti elettrici delle luci di pista, la creazione di nuove linee idrauliche di raccolta delle acque di piazzale, la sostituzione di tutte le luci di pista e di tutti gli aiuti visivi luminosi con segnali a tecnologia LED, l’ottimizzazione delle infrastrutture di volo con la creazione di un nuovo tratto di raccordo e l’ampliamento del piazzale Nord oltre che miglioramenti operativi di gestione degli aeromobili a terra. I lavori sulla pista si sono svolti in tre fasi. A marzo si è operato un intervento parziale, che non ha comportato limitazione dei voli, concentrato sul lato ovest e nell’area nord del piazzale aeromobili. Dal 26 aprile, sempre garantendo la continuità operativa, è stata avviata la seconda fase che ha interessato la testata est della pista. L’ultima fase si è invece svolta dal 13 maggio al 1° giugno e ha comportato la chiusura totale della pista. Per l’esecuzione dei lavori sulla pista, Sacbo ha investito 50 milioni, 9 dei quali per opere accessorie che comprendono gli impianti aeronautici di illuminazione (AVL). Un’opera senza precedenti di tale portata non poteva che essere effettuata da un’Associazione Temporanea di Imprese di alto livello come Vitali spa, a capo del gruppo, e Vallan Infrastrutture spa che si sono occupate della demolizione e della ricostruzione della pista e del piazzale, Impresa Edile Stradale Artifoni spa, che ha curato le opere idrauliche e, ultima, ma non meno importante, Carlo Gavazzi Impianti spa, che ha lavorato sugli impianti luminosi e di segnalazione.
Le macchine e le tecnologie
Come accennato, notevole l’apporto offerto da Bomag che ha messo a disposizione di Vitali due vibrofinitrici BF 800 C S500, due BF 800 C S600 oltre a un rullo gommato BW 27 RH-4i e quattro rulli tandem BW 174 AP-4i AM. Tutti i rulli erano equipaggiati con il sistema Asphalt Manager II, mentre le finitrici erano dotate del nuovo banco di stesa Magmalife. Infine tutte le macchine erano gestite dai sistemi Ecomode e Telematic. Una serie di tecnologie che ha permesso di seguire i ritmi serrati del cantiere scanditi da stringenti capitolati tecnici e da precise e tassative scadenze cronologiche. Senza queste tecnologie all’avanguardia di stesa, di compattazione e di monitoraggio del cantiere sarebbe stato difficile svolgere il tutto nei migliori dei modi e avrebbe certamente richiesto un dispiego aggiuntivo di forze e costi.
I banchi Magmalife, per esempio, presentano un nuovo sistema di riscaldamento che consente di risparmiare incrementando, allo stesso tempo, la sicurezza. Adottano piastre con resistenze in bagno di alluminio che assicurano affidabilità operativa e maggiore velocità di riscaldamento grazie all’elevata conducibilità termica di questo metallo. Inoltre questo sistema garantisce uniformità totale grazie alle lastre di alluminio che assicurano la perfetta distribuzione del calore su tutta la superficie della suola. «Le piastre – commenta Luca Guerra, Tecnico Bomag Italia specializzato in stese e finitrici – hanno resistenze in bagno di alluminio che, grazie all’ottima conducibilità, mantengono il calore a lungo facendo risparmiare anche in termini di carburante. Inoltre l’elevata conducibilità fa sì che nel banco non vi siano angoli freddi che potrebbero compromettere la stesa. Le finitrici erano dotate di sistemi di livellazione Moba. In particolare merita una citazione il Big Ski, un sistema di livellazione a 3 punti con asta di supporto in alluminio che ha permesso di evitare anche i più piccoli avvallamenti nella stesa per ottenere una planarità perfetta. Il suo facile utilizzo lo ha reso lo strumento preferito di ogni squadra».
Sul fronte della compattazione è risultato vincente il dispositivo Asphalt Manager II. «Si tratta – interviene Paolo Piroddi, Tecnico Bomag Italia specializzato in rulli e compattazione – della seconda generazione del nostro sistema di compattazione intelligente che rileva istante per istante il livello raggiunto adeguando in continuo l’intensità di vibrazione necessaria, ottimizzando così i tempi del cantiere, grazie a un concreto risparmio di tempo imputabile a inutili passate. Questo dispositivo evita inoltre le rotture del manto, che in un aeroporto significherebbero il completo rifacimento del lavoro». Un sistema che, tra l’altro, può essere utilizzato in modalità manuale da parte degli operatori più esperti, oppure in automatico venendo incontro alle esigenze degli addetti meno avvezzi a questa tipologia di macchine (e quindi ideale proprio per il noleggio).
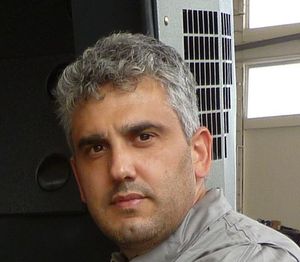
«Grazie a questa tecnologia innovativa – commenta Luciano Pasquali, Responsabile Assistenza Tecnica per Bomag Italia – è stato possibile l’avvicendamento di diverse squadre con una formazione davvero rapida. Non va inoltre dimenticato come Asphalt Manager vada sempre a chiudere l’asfalto indipendentemente dal senso di marcia del tamburo e questo contribuisce senza dubbio a incrementare la rapidità di compattazione».
Tecnologie che si devono inquadrare nella vastità del cantiere. In un lavoro come quello di Orio al Serio è infatti fondamentale gestire la situazione in modo rapido e assolutamente preciso. Per farlo, gli uomini di Vitali hanno potuto beneficiare del Bomag Telematic che permette di ottimizzare la gestione del cantiere, programmando i tempi di lavoro e di pausa di ciascuna macchina. Anche in un cantiere enorme come quello di Orio il sistema ha permesso di vedere a terminale (o da tablet) la posizione di ogni singola macchina in tempo reale monitorando in questo modo l’intero lavoro. Aggiunge Pasquali: «il Telematic permette di vedere le ore lavorate di ogni macchina per programmare la manutenzione durante i fermi. Inoltre il sistema è dotato di un report per visualizzare gli allarmi di errore che si possono presentare durante il lavoro e consente un intervento tempestivo di riparazione».
Merita infine un accenno anche l’Ecomode: il sistema di gestione intelligente della potenza di ogni macchina in funzione del reale fabbisogno operativo. Un dispositivo che consente grandi prestazioni con consumi di carburante e rumorosità ridotti al minimo e in linea con le contingenti necessità operative.
Le parole di Guerra sintetizzano appieno l’impegno di Bomag in questa occasione: «quello di Orio è stato senza dubbio uno dei cantieri più impegnativi che abbia mai affrontato. Fortunatamente la facile strumentazione e le macchine intuitive hanno permesso un perfetto adattamento delle squadre ai mezzi facendo filare tutto liscio come l’olio».
Impressionanti i numeri in gioco per un intervento straordinario di queste dimensioni. Le varie fasi hanno visto lavorazioni in continuo 24 ore su 24, su tre turni lavorativi e sette giorni su sette. L’area di pavimentazione oggetto dei lavori è stata pari a 550.000 m2 (oltre 80 campi di calcio, per dare un’idea dell’estensione), per più di 220.000 t di asfalto posato (corrispondenti a circa 6.500 autocarri da 34,5 t). È stata posata segnaletica orizzontale per oltre 56.000 m2, circa 295 km di cavi elettrici e sono state sostituite 2.000 luci di aiuto alla navigazione aerea. Con punte di oltre 300 addetti presenti in cantiere nella fase più impegnativa, dopo la riapertura dell’aeroporto si è provveduto alla stesa di ulteriori 45.000 m2 di asfalto.