Nel lotto più singolare del Brennero, sono i martelli demolitori EPIROC i veri protagonisti dello scavo
di Maurizio Quaranta
Siamo a Fortezza, a 19 km a sud di Vipiteno e a 11 km a nord di Bressanone, nella val d’I- sarco, dove il fondovalle è ampio solo alcune centinaia di metri; Fortezza è un importante nodo ferroviario che unisce la ferrovia della val Pusteria con la linea ferroviaria del Brennero, ovvero la val Pusteria con la val d’Isarco. Ma negli ultimi anni l’onore della cronaca è dovuto più che altro al fatto che da Fortezza parte la Galleria di Base del Brennero, l’elemento centrale della nuova linea ferroviaria del Brennero, che collega l’asse da Monaco a Verona; una volta completata, con i suoi 64 km di sviluppo, rappresenterà il collegamento ferroviario sotterraneo più lungo del mondo. A spingerci qui la curiosità di vedere all’opera i martelli demolitori di EPIROC, in particolare i modelli HB3100 e HB4100, utilizzati per lo scavo delle gallerie.
In particolare, ci stiamo dirigendo presso il Lotto “Sottoattraversamento Isarco”, quello che si posiziona più a sud dell’intera opera ed è stato affidato, a ottobre del 2014, al R.T.I. composto da Webuild S.p.A. (già Salini-Impregilo), Strabag AG, Strabag S.p.A., Consorzio Integra e Collini Lavori S.p.A.Le opere di questo lotto collegheranno la Galleria di Base con la linea ferroviaria classica del Brennero e la stazione di Fortezza; complessivamente saran- no realizzati 4,5 km di gallerie principali e 1,2 km di gallerie di interconnessione con la linea ferroviaria esistente. Più nel dettaglio, all’estremità sud della galleria di Base del Brennero all’incontro con l’attuale linea di montagna, il nuovo tracciato ferroviario deve transitare in uno spazio ridotto al di sotto dell’auto- strada, della strada statale e del fiume Isarco.
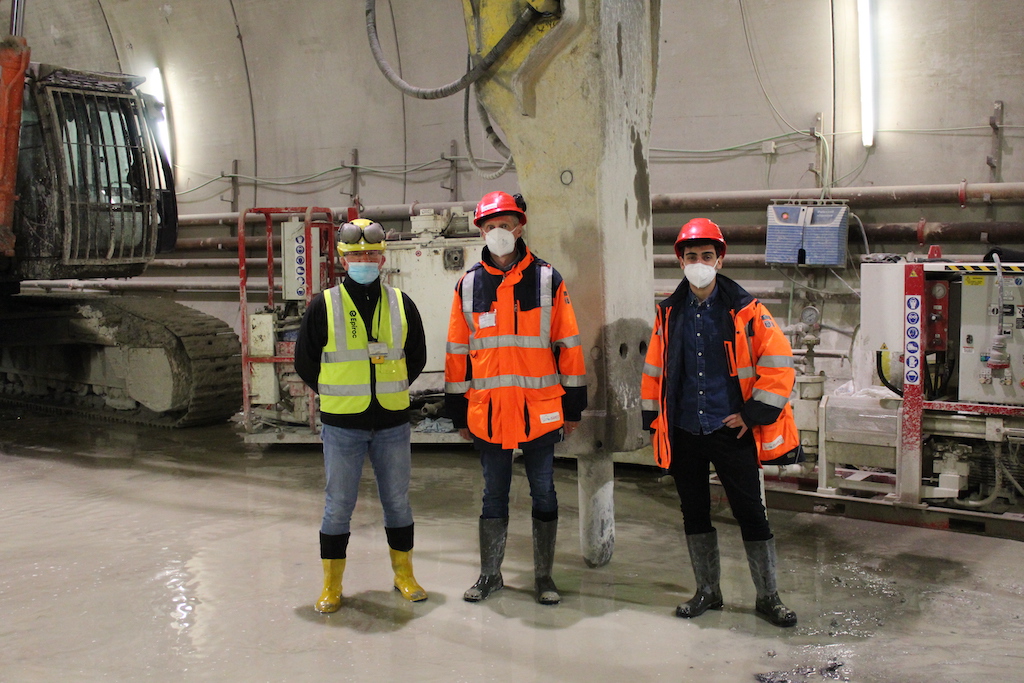
Il termine dei lavori di questo lotto è previsto nel 2023. Una volta entrati nel quartier generale operativo del Consorzio esecutore dei lavori, Isarco S.c.a r.l., è l’Ing. Simone Grosina, direttore di cantiere del lotto, a riferirci che “qui vi si trovano diverse caratteristiche geo- logiche e morfologiche che ne fanno uno dei lotti più complessi dell’intera opera. Terreno sciolto, materiali eterogenei, copertura ridotta, opere in falda, il fiume che attraversa il cantiere nonché le numerose sezioni di scavo imposteci dal progetto sono tutti aspetti che ci hanno indotto a non poter utilizzare frese o scavi meccanizzati, ma optare per l’applicazione di metodi di costruzione complessi come il jet-grouting – cioè l’iniezione nel terreno, sia verticalmente che orizzontalmente, di una miscela cementizia ad alta pressione attraverso piccoli ugelli al fine di consolidare i terreni e facilitarne lo scavo – la tecnica del “congelamento” del terreno – una procedura impiegata nell’ambito delle opere in sotterraneo, dove il suolo viene con- gelato artificialmente, rendendolo compatto e im- permeabile – e lo scavo in tradizionale coi martelli demolitori EPIROC”.
Una realizzazione complessa
Ma prima di dedicarci ai martelli demolitori EPIROC HB, vediamo di conoscere un po’ meglio il cantiere del lotto in questione.
Come già detto, la realizzazione dei lavori è tecnicamente molto complessa: le gallerie delle canne principali e delle interconnessioni passeranno infatti al di sotto del fiume Isarco, dell’autostrada A22, della strada statale SS12 e della linea ferroviaria storica Verona-Brennero. “Al fine di lavorare in sicurezza ed in modo sostenibile, evitando lo spostamento del fiume dal suo corso naturale, in fase progettuale – continua Grosina – abbiamo optato per adottare la tecnica congelamento del terreno con azoto liquido, poiché il congelamento del guscio di terreno intorno alla sagoma delle gallerie permette lo scavo pur in presenza di importanti battenti d’acqua”.
Del resto, l’attenta gestione delle risorse naturali è un elemento fondamentale della progettazione e della realizzazione della Galleria di base del Brennero. Adottando idonee misure di mitigazione BBT SE – la società per azioni europea finalizzata alla realizzazione della galleria ferroviaria tra Italia ed Austria, ovvero la Galleria di base del Brennero – è impegnata a minimizzare l’impatto che i suoi interventi generano. Inoltre, sono in fase di attuazione, di concerto con gli enti territoriali dell’area di progetto, una serie di misure di compensazione ambientali.
I 4 pozzi
In seguito al consolidamento del terreno dall’alto con la tecnica del jet-grouting, sono stati scavati 4 pozzi– due per ogni lato del fiume, con diametro di 60-80 metri – tramite i quali è stato possibile raggiungere la quota del tracciato delle gallerie, ad una profondità di circa 25 metri, da cui sono stati avviate le attività di consolidamento in orizzontale e di perforazione propedeutica al congelamento del terreno nonché gli scavi in sotterraneo, sempre con metodo tradizionale.
“Partendo da uno dei quattro pozzi realizzati nel cantiere del Sottoattraversamento dell’Isarco sono stati congelati – ad intervenire è ora l’ing. Emanuele Matteucci, plant manager del cantiere – la falda e il materiale alluvionale al di sotto dell’alveo del fiume, iniettando azoto liquido all’interno di un circuito aperto, costituito da tubazioni di congelamento o sonde, sotto il fiume”.
L’azoto, con una temperatura di –196°C, scorrendo all’interno di queste tubazioni ha sottratto il calore dal suolo circostante e l’acqua all’interno del suolo sotto al fiume si è congelata, permettendo alla temperatura del suolo di scendere al di sotto dei –35°C. “Grazie al metodo del congelamento – continua Matteucci – è stato possibile evitare di dover spostare il percorso del fiume che attraversa il tracciato della Galleria di base del Brennero e ridurre gli impatti ambientali, in particolare sulla fauna ittica dell’Isarco. La tecnica si sta rivelando tecnicamente appropria- ta per la specifica applicazione ed è stato in questo modo possibile consolidare il materiale sciolto al di sotto dell’alveo del fiume, avviando i lavori di scavo”. Una volta congelato il terreno tutto attorno al profilo della galleria, si è provveduto ad avviare l’attività di cavo vera e propria con la tecnica dello scavo in tradizionale.
Entrano in gioco i martelli demolitori
Ed è qui che sono entrati in gioco i martelli demolitori EPIROC HB, montati rispettivamente su Hitachi490 l’HB4100 e su Hitachi350 l’HB3100. “Qui i martelli demolitori non li usiamo per attività di complemento, ma il ricorso al martello è l’unica tecnica utilizzata per lo scavo di queste quattro gallerie. Qui – ancora Matteucci – l’HB4100 e l’HB3100 sono veri e propri martelli di produzione e di scavo. Per essere precisi i martelli, ma quelli molto più piccoli, li utilizziamo anche per lavori più fini, quando è necessario profilare o rifinire in modo corretto senza danneggiare quello che abbiamo già portato a termine”. Infine, la galleria scavata sotto il fiume verrà rivestita con idonee membrane impermeabili e calcestruzzo armato per proteggerla dalle infiltrazioni d’acqua.
“In cantiere abbiamo ben 9 martelli EPIROC di varie taglie, (NDR. a cui presto se ne andranno ad aggiungere altri due). In particolare, abbiamo due martelli per macchina, perché il martello è uno strumento fondamentale cui non possiamo fare a meno, è insostituibile nel nostro ciclo produttivo. Non possiamo permetterci di interrompere lo scavo a causa di un qualsiasi problema al martello; dietro l’escavatore con martello – continua Matteucci – vi è infatti tutta una sequenza di lavorazioni che debbono procede- re a ritmo serrato con l’utilizzo di uomini e materiali. Qui le perdite di tempo sono irrecuperabili, non c’è modo di compensarle. Ne consegue che per noi non si tratta per noi di semplice fornitura, ma si tratta di un vero e proprio servizio quello reso da EPIROC e i suoi martelli demolitori”.
Nell’ambito del contratto completo di manutenzione e di fornitura di pezzi di ricambio, EPIROC si impegna a garantire un funzionamento senza problemi con tempi di fermo macchina minimi; il contratto di fornitura dei martelli e della manutenzione include il servizio di riparazione e manutenzione con personale operativo 24 ore su 24, 7 giorni su 7, per garantire disponibilità, produttività, efficienza e allungamento della vita tecnica del martello.
È l’ing. Christian Maggioni, Regional Business Line Manager HAT (Hydraulic Attachment Tools), a riferirci invece che da 50 anni a questa parte “con l’introduzione del demolitore idraulico senza falsa modestia – sempre Maggioni – possiamo dire di aver trasformato il settore dell’ingegneria civile e mineraria: con le nostre due gamme, la Premium a colpo variabile e la EC a colpo fisso (e di colore grigio), siamo ora in grado di coprire con efficienza e prestazioni elevate, rumorosità e vibrazioni ridotti ogni esigenza della nostra clientela e trasformare ogni escavatore di 0,7-140 tonnellate in uno strumento versatile per operazioni di demolizione, scavo nella roccia, estrazione in miniere e molte altre applicazioni”.
Un demolitore all’altezza del compito
Molte sono le caratteristiche che rendono questo utensile, fabbricato in Germania, la macchina giusta per questa particolare attività: il design robusto, la lunga durata di tutti i componenti del demolitore HB, il sistema di ingrassaggio automatico ContiLube II, la sella nebulizzata e il sistema EnergyRecovery, che utilizza l’energia generata dall’estensione del pistone per ridurre l’usura e le vibrazioni sul veicolo portante. Inoltre, il DustProtector, il sistema di tenuta antipolvere con boccola flottante, che rimuove le particelle più grandi, e il filtro per rimuove la polvere più sottile e le particelle di sporco, impedendo così che particelle estranee entrino nel demolitore idraulico. Infine, il sistema IPS (Intelligent Protection System) che coniuga tra loro in modo perfetto le famose funzioni AutoControl e StartSelect di EPIROC: il sistema rende il lavoro ancora più semplice adattando automaticamente il comportamento operativo del martello demolitore a qualsiasi condizione di lavoro.
La produttività aumenta in quanto, con la sua funzionalità completamente automatizzata, il sistema IPS non richiede alcun intervento da parte dell’operatore e dunque non ci sono interruzioni del lavoro; il sistema assicura un posizionamento più accurato e notevolmente più veloce del demolitore, grazie all’effetto di centraggio ed evita i colpi a vuoto che spesso danneggiano l’utensile. Ciò elimina inoltre le sollecitazioni meccaniche sulla macchina portante e prolunga la vita utile di tutti i componenti soggetti all’usura.
Tutto sotto controllo con la nuvola
Ad aumentare la produttività dei demolitori EPIROC si è aggiunto di recente HATCON (Hydraulic Attachment Tools Connectivity), un dispositivo di monitoraggio remoto per demolitori e frese a tamburo che tiene traccia della posizione e delle ore di funzionamento per migliorare l’efficienza e la sicurezza.
La piattaforma basata su cloud My Epiroc fornisce ai clienti notifiche sulla manutenzione, crea elenchi di attività e fornisce una panoramica completa dell’intera flotta.
Tutti i dati vengono presentati in modo diretto per semplificare sia le attività quotidiane che le decisioni a lungo termine. “HATCON fornisce un nuovo livello di controllo – ha spiegato Christian Maggioni–. Saprete sempre dove sono i vostri utensili, cosa fanno, quando hanno bisogno di manutenzione, se un utensile viene utilizzato più degli altri, fondamentalmente vi tiene sempre aggiornati.
E con My EPIROC, tutto, dalla pianificazione della manutenzione, all’identificazione dei guasti e alla ricerca di nuove soluzioni sarà molto più facile e veloce. Queste informazioni non solo contribuiranno a creare un flusso di lavoro più fluido con meno tempi di fermo macchina, ma possono anche essere fondamentali per raggiungere gli obiettivi aziendali”.
HATCON è disponibile di serie o come kit retrofit per demolitori e frese a tamburo di gamma premium EPIROC permette di poter accedere alle agevolazioni fiscali previste dalla INDUSTRIA 4.0.