Una membrana riflettente in grado di catturare energia, una struttura portante rigida e leggera al tempo stesso, un sistema di prova che sfida la calura del nord Africa. Come si è realizzata la start up di Airlight Energy, grazie a menti geniali e molta determinazione
Airlight Energy ha recentemente ultimato un impianto termodinamico ad Ait-Baha, nei pressi di Agadir, in Marocco: un’opera altamente innovativa e sicuramente all’avanguardia nel campo delle energie alternative.
La struttura è integrata nel cementificio di proprietà della Ciments du Maroc (Gruppo Italcementi) ed è stata totalmente progettata da Airlight Energy.
Dire «progettata» è in un certo senso riduttivo perché in questo caso si è trattato di un’invenzione rivoluzionaria in cui creatività, fantasia, competenza tecnica, uso innovativo dei materiali hanno concorso alla realizzazione di un progetto che, mutatis mutandis, si inerisce a buon diritto nelle ardite intuizioni tecnologiche che hanno connotato il nostro Rinascimento.
Perché non è certo di tutti i giorni impiegare una membrana alluminizzata genialmente saldata per catturare l’energia, l’aria come vettore termico, il calcestruzzo al posto del metallo e un sistema che utilizza sassolini per lo stoccaggio dell’energia.
Un’avventura (avvincente e vincente) alla quale hanno contribuito attrezzature di prova di prim’ordine e due laboratori all’avanguardia, uno in Svizzera e un altro, mobile, in Marocco. Per capire come sono andate le cose ci siamo recati a Biasca, in Svizzera, nella sede di Airlight Energy.
Tutto nasce da una membrana
Come spesso succede, le scelte vincenti si basano su concetti semplici: in seguito a una richiesta partita da un’Università australiana per uno studio sulle energie rinnovabili, i tecnici di Airlight Energy si sono chiesti (forse pensando agli specchi ustori di Archimede…) se non si potessero utilizzare membrane completamente riflettenti per concentrare l’energia solare in un «fuoco».
Sono quindi nati una serie di prototipi (al ritmo di uno ogni due anni) e di brevetti (circa 50) volti a creare il cosiddetto CSP, Concentrated Solar Power che, tramite un sistema di specchi, convoglia l’energia solare in un punto, utilizza l’aria come medium (in alternativa all’olio diatermico o ai sali fusi) e produce calore che poi viene immagazzinato in un sistema di stoccaggio oppure direttamente dirottato verso uno scambiatore che crea vapore e alimenta la turbina. Nasce così l’energia elettrica.
La grande novità di questa intuizione sta nel fatto che si utilizza una membrana in poliestere alluminizzata e saldata in tre rotoli in modo che si possa avere uno specchio riflettente di dimensioni molto grandi e in un materiale alternativo al vetro (troppo fragile e difficile da pulire) o l’alluminio. In questo modo si è in grado di concentrare 200 soli contro i 50 convenzionali.
Il cimento dell’invenzione
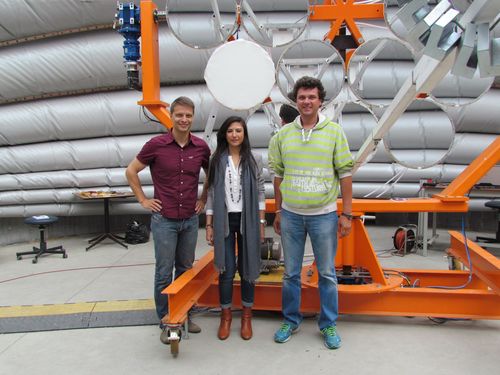
«In un primo tempo si pensava di lavorare con uno specchio solo e di dargli una forma mettendolo in tensione con pressioni negative in modo da concentrare i raggi del sole in un punto», ci ha spiegato il dott. Giovanni Martinola, responsabile del dipartimento di Scienze dei Materiali di Airlight Energy e docente di tecnologia del calcestruzzo al Politecnico Federale di Zurigo. «Ma in questo primo prototipo la distanza tra il punto di focalizzazione e la membrana era eccessiva e il receiver era estremamente esposto alla temperatura ambiente e agli agenti atmosferici. Dovevamo proteggere il receiver, limitare le perdite di calore e portarlo all’interno della membrana vicino allo specchio in modo da poter controllare completamente le perdite, dovute anche al doppio passaggio della luce attraverso la stessa».
Si è quindi passati a un altro prototipo, un collettore costruito come una tensiostruttura in una membrana in ETFE quasi completamente trasparente usata da anni nelle serre olandesi e in agricoltura, un polimero autopulente, estremamente resistente, trasparente su tutto lo spettro della luce.
Un passo avanti, ma non quello definitivo. Per ottenere il risultato ottimale occorreva perfezionare la geometria dello specchio, approssimandone la forma a una parabola in modo da concentrare la luce riflessa in un unico punto, senza l’ausilio di uno specchio secondario.
Nasce così la versione finale che porta in sé un’altra sorprendente idea: l’utilizzo del calcestruzzo (invece che l’acciaio o dell’alluminio) come materiale portante di tutto il sistema ottico.
Il sogno si realizza e oggi, nel 2014, i progetti lasciano il posto a un impianto reale, quello della Ciments du Maroc, una cementeria realizzata nel 2010 al cui fabbisogno energetico contribuiscono gli specchi e i collettori di Airlight Energy.
Leggerezza e stabilità
Airlight Energy ha nel suo dna la progettazione di strutture rigide ma al tempo stesso leggere nel campo dell’edilizia, sul modello dell’Allianz Arena di Monaco, della stazione di Montreaux, della Sala Tropicale dello zoo di Zurigo: una leggerezza progettuale che però non è mai e disgiunta dalla portanza strutturale. Deve quindi aver fatto tesoro delle precedenti esperienze quando ha scelto il calcestruzzo per la struttura portante dei collettori, anche questa parte di un percorso di ricerca interno.
Ovviamente non si tratta di un materiale convenzionale ma di calcestruzzo autocompattante fibrorinforzato, in cui parte dell’armatura è integrata, con proprietà meccaniche tre volte superiori a un calcestruzzo RCK 30 utilizzato nel 95% dei casi in Italia e quindi questi calcestruzzi ad alte performance devono essere controllati in modo adeguato.
Sono stati utilizzati dei casseri nuovissimi completamente chiusi, composti da tante fusioni di alluminio accoppiate per avere la possibilità di ottenere forme non convenzionali, tanti piccoli pezzi di Lego sfornati nel minor tempo possibile e poi assemblati. Il calcestruzzo autocompattante viene messo in opera senza l’ausilio di energia di compattazione esterna e viene pompato da due bocchettoni che si trovano nella parte inferiore del cassero: il riempimento del manufatto (circa 23 m cubi di cls) richiede circa 15 minuti, mentre i tempi di indurimento sono decisamente ridotti.
Geni da laboratorio
«Il nostro compito è quello di controllare le materie prima in entrata (il mondo degli aggregati, dell’additivazione liquida e dei leganti idraulici) componenti che, una volta miscelati con l’acqua, fanno il calcestruzzo», afferma il dott. Giovanni Martinola. « Su questi materiali eseguiamo circa una trentina di prove. Nel caso specifico dell’impianto in Marocco, poiché per i supporti dei collettori utilizziamo calcestruzzo autocompattante e quindi i pezzi devono essere perfetti dal punto di vista estetico, senza bolle, senza nidi di ghiaia, l’aerologia è stata controllata per ogni carico di produzione per raggiungere l’omogeneizzazione ottimale del materiale».
Le prove sono ovviamente molto delicate e complesse, richiedono molta attenzione, (si lavora con strumenti che misurano 0,1 micron), ma sono fondamentali per poter determinare dal punto di vista meccanico e strutturale la portanza del calcestruzzo.
Negli ultimi mesi Airlight Energy sta valutando e cercando di brevettare materiali fibrorinforzati con resistenze a flessotrazione vicino a quelle dell’alluminio, un obiettivo impossibile da raggiungere fino a poco tempo fa, visto che il divario tra il comportamento a trazione di una lega in alluminio e il calcestruzzo era enorme.
In laboratorio abbiamo notato anche una pressa che potenzia il lavoro dell’Advantest, costruita da Airlight Energy ad hoc per la determinazione di resistenze a compressione cubiche dell’ordine di 500/600 Mega Pascal, dieci volte superiori a quelle dei calcestruzzi standard. Inoltre, visto che l’Advantest permette il collegamento con più telai, in Airlight Energy stanno pianificando l’acquisto di altri telai per poter fare prove a flessione su travetti e su piastra e per poter quindi caratterizzare il materiale anche dal punto di vista della sua duttilità e deformabilità.
In Airlight Energy esprimono piena soddisfazione per l’Advantest e per la Casa produttrice della macchina, la Controls.
«I rapporti con Controls sono ottimi», spiega Martinola. «Si tratta di un’azienda dinamica, disponibile, competente, che non abbandona il cliente una volta venduta la macchina. Abbiamo molto apprezzato anche la loro flessibilità e il loro supporto alle nostre integrazioni di prodotto e le tempistiche di fornitura, oltre all’ottimo rapporto qualità/prezzo. Oltretutto sono particolarmente attenti all’evoluzione normativa, tutte le novità vengono immediatamente recepite e le macchine subito adeguate. Il prodotto così come è stato studiato è esattamente il prodotto che va per noi».
Airlight Energy è una società privata svizzera che offre soluzioni a elevata tecnologia nel campo dell’energia solare rivolte alla produzione su larga scala di elettricità, energia termica e stoccaggio di energia. Nata nel 2007 e ubicata a Biasca, in Svizzera, impiega una sessantina di addetti, annovera una cinquantina di brevetti depositati e ha segnato il suo passaggio dalla fase di start up a quella commerciale con l’imponente progetto dell’impianto solare di Ait Baha, in Marocco,che entro il 2020 avrà una capacità produttiva di 2000 MW: un’applicazione industriale destinata a essere una pietra miliare nel settore delle tecnologie solari. Numerose le partnership scientifiche e commerciali che hanno connotato i primi sette anni di vita di Airlight Energy: tra essi il Paul Scherrer Institut, Energie Schweiz, il politecnico di Losanna, l’Eni. Con IBM Airlight Energy sta mettendo a punto un innovativo sistema che utilizza l’energia solare, in grado di generare fino a 2000 soli e di fornire, con una sola unità, elettricità, acqua calda, acqua desalinizzata, aria condizionata. In Airlight Energy si portano avanti anche parecchie sperimentazioni sull’utilizzo di nuovi materiali: per quanto riguarda il calcestruzzo per esempio, è in fase di test un nuovo tipo di materiale, simile al metallo, con innovative caratteristiche di flessione e duttilità. Tra gli ambiti applicativi delle soluzioni proposte da Airlight Energy, oltre a quello industriale (industrie energivore, cementerie, cartiere…) l’agricoltura, le costruzioni, la desalinizzazione dell’acqua
I laboratori mobili in situ spesso sono considerati una postazione di seconda mano, una succursale di quelli fissi, ritenuto ingiustamente più blasonati. Non è così nel caso del laboratorio mobile di Airlight Energy in Marocco, ospitato in un container da 40 piedi e utilizzato per le prove di qualità che, annovera, tra le altre attrezzature, l’Advantest di Controls, il secondo che l’azienda ha acquistato. Dal punto di vista della tecnica di laboratorio qui per la prima volta è stata integrata in una postazione mobile una macchina complessa come l’Advantest per eseguire prove della meccanica della frattura in controllo di deformazione «La qualità in questo contesto è fondamentale – ha spiegato il Dr. Giovanni Martinola, responsabile del Dipartimento Scienze dei Materiali di Airlight Energy e docente di tecnologia del Calcestruzzo al Politecnico federale di Zurigo. « Abbiamo quindi bisogno di attrezzature particolarmente affidabili visto che ad Ait – Baha la struttura è stata sollecitata al massimo della capacità, per un totale di 50 compressioni e 20 pezzi prodotti al giorno». Il sistema computerizzato servo controllato per telai di prova Advantest di Controls esegue in modo automatico prove statiche e dinamiche a bassa frequenza su materiali da costruzione. È azionato da una pompa idraulica a doppio stadio con motore AC combinato con valvola proporzionale servo controllata a loop chiuso e algoritmo P.I.D. proprietario. Si tratta di un sistema flessibile, affidabile, adatto sia per prove tradizionali che avanzate.
I vantaggi di Advantest: consente di eseguire in modo automatico prove statiche e dinamiche a bassa frequenza in controllo di carico, spostamento e deformazione, ampiamente personalizzabili dall’operatore; permette di modificare a prova in corso la variabile di controllo (carico, spostamento, deformazione), la velocità, il target e tutti i parametri di retroazione; algoritmo di controllo P.I.D. proprietario ottimizzato in rapporto alle caratteristiche oleodimaniche del sistema per ottenere prestazioni e precisione del controllo eccellenti; esecuzione di prove di compressione, flessione e di trazione indiretta; determinazione del modulo elastico secante e test in controllo di spostamento / deformazione su calcestruzzi fibro – rinforzati (FRC-FRP) e proiettati secondo le principali norme internazionali; disponibile anche nella versione ROCK per l’esecuzione automatica di prove monoassiali, triassiali standard e triassiali Stress-Path su carote di roccia; precisione e affidabilità nel tempo anche in condizioni di lavoro intensive; visualizzazione grafica e numerica in tempo reale di tutte le grandezze di prova; linearizzazione software delle curve di calibrazione di tutti i trasduttori. Grazie ai suoi plus, Advantest rappresenta la soluzione ideale per laboratori centrali e centri di ricerca, ottimizzato per il controllo sia di telai di prova Controls, sia per telai esistenti di altra origine.
La saldatura delle strisce di membrana alluminizzata è il colpo di genio che ha fatto sì che si potesse disporre di superfici adeguatamente ampie per coprire la parte ottica. I film in ETFE (Etilene tetrafluoroetilene) di circa 1 metro e mezzo vengono saldati fino a raggiungere i 212 metri necessari, esattamente la larghezza del collettore. Anche se la stesura del telo avviene in modo automatico, con l’ausilio di due macchine saldatrici LAEM System Cutting Edge Technology, è sempre necessario un controllo manuale per verificare che non vi siano sovrapposizioni e grinze e tutto proceda per il meglio. Una volta saldati i rotoli vengono assemblati, caricati e inviati in Marocco