“Kaizen” è una parola giapponese formata dai termini Kai (cambiamento) e Zen (meglio). Ha rappresentato per oltre 70 anni una “Filosofia di Business” pilastro del successo economico non solo del Giappone, ma anche degli Stati Uniti. In sintesi, è un processo quotidiano di miglioramento della qualità e di semplificazione del lavoro, basato su una progressiva ma continua “spinta al miglioramento dal basso”, in quanto sono tutte le persone che lavorano su una linea o reparto, di ogni settore e livello, a definire ed mettere in atto i cambiamenti che migliorano il loro lavoro; alla Direzione spetta il compito fondamentale di supportare ed incentivare i team kazien, fornendo loro le risorse necessarie.
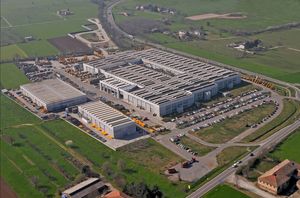
Ma è possibile l’applicazione del Kaizen, quindi della “cultura del miglioramento” a una realtà industriale? Non solo è possibile, ma è il cambiamento già in atto: la Dieci srl di Montecchio Emilia ha dato il via al proprio “Progetto Kaizen”, ennesima tappa della continua tendenza all’innovazione che è filosofia portante dell’azienda emiliana. Gli stabilimenti Dieci si estendono su oltre 120.000 metri quadri, incluso un moderno Campo Prove, Magazzini, Centri di Ricerca, e tutto il necessario al funzionamento di una grande azienda metalmeccanica, che produce Elevatori Telescopici, Dumper, Betoniere e Macchine Speciali per Edilizia e Agricoltura, in 9 linee di montaggio a cui si aggiungono 4 reparti di completamento, oltre a 2 reparti di carpenteria, 2 reparti di verniciatura e 4 reparti di pre-montaggio. L’estensione stessa degli stabilimenti e la distribuzione dei mezzi di produzione (con l’organizzazione del lavoro “tradizionale”) comportava per forza di cose frequenti spostamenti dei lavoratori e delle macchine con conseguenti intralci, sprechi e ritardi. Senza contare gli imprevisti (pur fisiologici in ogni azienda) come rotture di macchinari, difetti, conseguenti riparazioni, ripercussione dei ritardi lungo tutta la catena di produzione e stress fra gli operatori.
Per mezzo del Kaizen, tutto questo cambierà: le “vecchie” linee ed i 4 reparti a valle (secondo il criterio di razionalizzazione e standardizzazione), stanno per cedere il passo a 6 moderni “Canali di flusso integrati” da cui uscirà il prodotto finito, pronto per la spedizione. Ogni stazione dei Canali di Flusso avrà i propri addetti, alimentati dei materiali necessari su appositi carrelli: niente più interruzioni, quindi, per ricercare il materiali, e niente più materiali che ingombrano la zona di lavoro, con conseguenti perdite di tempo, e situazioni di disagio per i lavoratori.
L’insieme degli operatori di ogni Flusso sarà in effetti un vero e proprio “Team”, capace di proporre cambiamenti e miglioramenti, analizzare eventuali problemi, e risolverli di concerto con i Leader degli altri Flussi e i Responsabili di ognuno dei 5 gangli vitali dell’Azienda: Personale, Ufficio Acquisti, Ufficio Commerciale, Ufficio Tecnico e Direzione. I Meeting quotidiani e periodici (Daily e Weekly Kaizen) fra gli Operatori e i Responsabili di Flusso diverranno la norma, sia per potenziare la comunicazione “dal basso all’alto”, che per analizzare i problemi rapidamente, raccogliere suggerimenti e applicare le risoluzioni operative, da subito. Eventuali migliorie verranno poi raccolte e analizzate nella riunione successiva, in quel “cerchio” senza fine di lento ma continuo miglioramento che è il fondamento della filosofia. Ovviamente tutto questo non si crea dal nulla: la Formazione di ogni livello del personale (da sempre fiore all’occhiello Dieci) sarà incrementata: primo obiettivo sarà la creazione di quello “spirito di squadra” necessario al cambiamento, e contemporaneamente la formazione Tecnica per l’adozione delle nuove tecnologie applicate ai Flussi di lavoro.